WEAVING RUGS IN THE HIMALAYAS
​


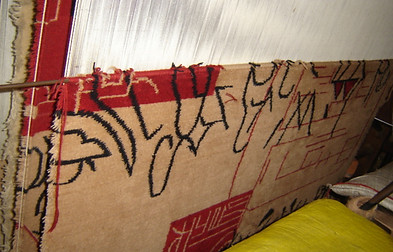
Tibetan/Nepalese Rug Story
The art of rug weaving in the Himalayan region is part of an age old tradition practiced primarily for use in the home. Originally rugs were produced for mats, door covers, horse sadlles, bed covers and pillar rugs which were placed around columns in Buddhist temples. Traditional Tibetan weavings generally reflect the influence of the Buddhist religion in Tibetan culture and art.
After the invasion by China in 1959, Tibetans fled as refugees and settled in Nepal & India. To make a living in a foreign land, rug weaving began again in Tibetan refugee camps primarily in Pokhara and the Kathmandu valley of Nepal. By the mid 1970's rugs made by Tibetans living as refugees in Nepal were being exported to Europe in small quantities. In 80's export boomed of Nepalese rugs to Europe mainly to Germany becoming the top export of the country. After the much acclaim in Europe, Tibetan/Nepalese rugs began to receive increasing attention in the United States. First limited to art collectors, antique dealers and interior decorators, Tibetan/Nepalese rugs have now caught the interest of many Americans who realise the exceptional value and durability of the rugs. Due to their handcrafted appearance, highly stylized patterns and beautifully matched color schemes, American public have come to appreciate the real beauty of these rugs.
​
Today Tibetans and local Nepalese have begun to expand their artistic horizons. Patterns from other Persian, Turkish, European, and Southwestern motifs are now increasingly used by Tibetan artisans in addition to contemporary designs which are becoming popular. In addition, weavers have started working closely with the consumers to bring life to individual designs and color schemes.
Whatever their ethnic origins, Tibetan/Nepalese rugs have a compelling simplicity complimented by a color spectrum spanning from the rich reds and blues to the soft lavenders and grays. Both natural vegetable and synthetic dyes are used to enrich the artisans palette of colors.
​
How Himalayan Rugs are made
Weaving a rug the traditional Himalayan way requires hand-processing carefully chosen raw materials - wool and hand-weaving often complex designs using a technique that is unique simple.
Wool
First step in rug making by skilled artisans begins on the high grasslands of the high Himalayan plains. Sheep from these plains are adapted to the harsh climate by growing wool that consists of long fiber, exceptional durability, softness and remarkable lustrous quality.
​
Rugs made from Himalayan wool actually grow more beautiful as time passes by, developing a silk-like sheen with age and use. The Himalayan after shearing by hand first cleaned and carded, then spun by hand into yarn that will become a rug.
​
Dyeing
After the wool has been spun, it is dyed according to the colors required in the designs. This important part of the rug-making process is, in itself, a highly developed craft. Since ages, Tibetan dye masters have learned a deep knowledge of the natural materials that could be used to create dyes for the rich palette of colors for the demanding rug market. Natural herbal plants included indigo, mulberry, saffron, turmeric, rhubarb root, walnuts, camellia tea, and many more. These days chemical dyes are increasingly used in dyeing yarns. Fortunately, chemical dyes have come a long way and when used properly, they dyes are almost completely absorbed into the wool, are color-fast and leaving very few residuals in the waste water.
Weaving
After preparing dyed yarns, the weaving process can begin. Tibetan rugs are woven on simple vertical looms on which the warp (the vertical threads that form part of the skeleton of the rug, usually cotton) is wound.
​
The pile of the rug is created by looping yarn around two warp threads, and then around a guide rod that lies perpendicular to the warp. The looping continues until the end of a row is reached. Once a row is completed, the rod is hammered tight against the row below. The weaver then cuts along the rod with a very sharp knife, cutting open the pile. The rod is removed and the row is beaten down against the previous row once again. The two or three weft threads are then inserted along the top of the row, the weaver slides the metal rod back in above the weft, and a new row is started. This knot is known as a Senna loop. Rug weaving in central Asia east Asia use the Persian or Turkish knotting, in which each knot is tied, trimmed, and packed before the next one is started, resulting in knots that are square, elongated and continuous. Senna loops are tied off only when the weaver changes color or reaches the end of a row. These days many weaving combination such as loop/cut, higher pile/lower pile, silk/wool and natural fiber/wool are used in weaving Tibetan rugs and they are gaining popularity.
​
Finishing
After the weaving process is complete, it is taken off the loom and trimmed to smoothen the surface and remove any irregularities in the height of the rich pile. The trimmers may works up to a week trimming each rug to ensure that it attains the highest possible quality. After trimming completed, rugs are washed with natural herbs & water to fix the colors and give shine to the rugs. The rugs are then are dried in the open sun & air. Once dried completely they are once more trimmed and cleaned before packing.
We hope this brief Rug Story has enlightened you on rug weaving the Himalayan way......
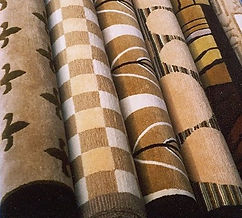
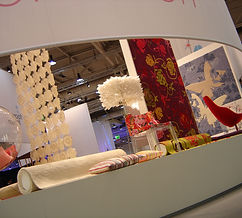